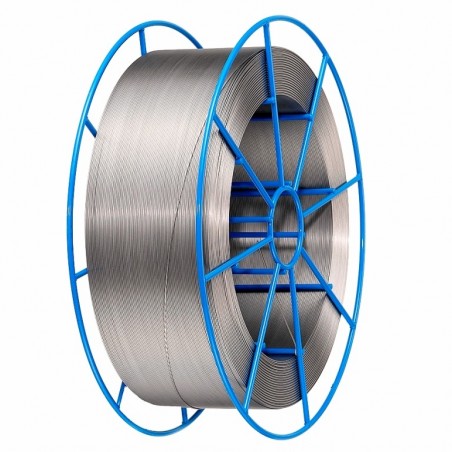
Stainless steel wire Rope 316 Ø 0.81 mm - 0.13Kg 50 meters Stainless steel...
Réf : 0013148
In MIG welding, the solid stainless steel wire is a filler material or welding wire: It's used for joining thick stainless steel parts, making it suitable for filling. The 316L stainless steel is resistant to corrosion in acidic environments.
MIG welding, known for its speed and efficiency, is an arc welding method that stands out for its simplified approach while requiring specific technical expertise. In this process, the solid stainless steel wire plays a key role as a filler material, particularly suited for welding on thick stainless steel parts. This method is ideal for the effective filling of joints, ensuring strong and durable welds.
The use of 316L stainless steel as a filler material in MIG welding is a preferred choice due to its high resistance to corrosion, especially in acidic environments. This feature makes 316L stainless steel perfect for applications in demanding environments, such as the chemical or marine industries, where materials are regularly exposed to corrosive substances.
The MIG technique is characterized by the automatic and continuous feeding of the welding wire, allowing the operator to maintain a uniform and uninterrupted welding operation. This continuity is crucial to ensure the quality and consistency of welds over long periods. Moreover, MIG welding uses a protective gas atmosphere, typically a mixture of argon and carbon dioxide, to preserve the purity of the weld by preventing any interaction with the ambient air.
In summary, MIG welding with solid 316L stainless steel wire combines speed, simplicity, and precision while offering exceptional resistance to corrosion. This technique stands out as a reliable solution for professionals looking to achieve high-quality welds in challenging conditions.
Stainless steel wire Rope 316 Ø 0.81 mm - 0.13Kg 50 meters Stainless steel...
Réf : 0013148
Stainless steel MIG welding wire 316LSi - Ø 0.8 mm - V4A - 1.4430, 5.00Kg...
Réf : 0009822
Stainless steel TIG welding wire 1.4430 - Ø 1.2 mm - 316LSi 5.00Kg 560...
Réf : 0012005
Stainless steel TIG welding wire 1.4430 - Ø 0.8 mm - 316LSi 0.120Kg 30...
Réf : 0012740